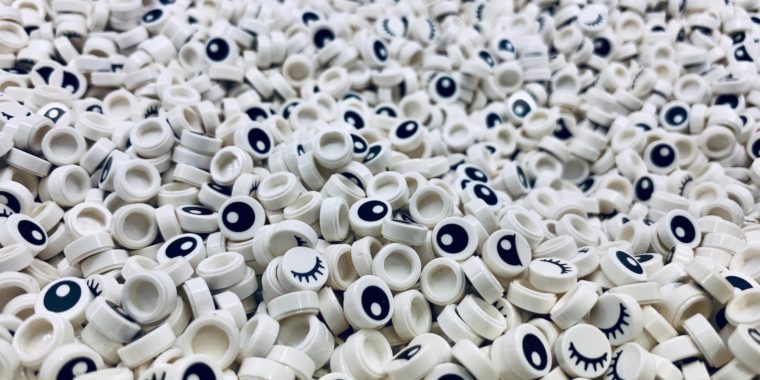
Przemysł 4.0 to nowa era produkcji, w której cyfrowe technologie rewolucjonizują sposób, w jaki produkujemy i dostarczamy do klientów nasze towary. Dzięki wprowadzeniu innowacyjnych rozwiązań takich jak sztuczna inteligencja, robotyka czy Internet Rzeczy, efektywność i jakość produkcji osiągają zupełnie nowy poziom. Procesy stają się bardziej zautomatyzowane, precyzyjne oraz elastyczne, co przekłada się na większą wydajność i satysfakcję zarówno dla przedsiębiorstw jak i konsumentów.
Internet Rzeczy w Akcji – jak połączone maszyny optymalizują procesy produkcyjne?
W dzisiejszych czasach cyfrowa rewolucja dotknęła praktycznie wszystkie dziedziny życia, a produkcja nie jest wyjątkiem. Jednym z kluczowych elementów tej rewolucji jest Internet Rzeczy (IoT), który umożliwia komunikację i współpracę między różnymi urządzeniami i systemami. W fabrykach można teraz znaleźć połączone maszyny, które są w stanie optymalizować procesy produkcyjne.
Dzięki IoT maszyny mogą zbierać dane na temat swojej pracy oraz środowiska, w którym się znajdują. Te informacje są następnie przesyłane do centralnego systemu, gdzie są analizowane przy użyciu zaawansowanych algorytmów. Dzięki temu możliwe jest monitorowanie efektywności poszczególnych maszyn oraz identyfikacja potencjalnych problemów lub awarii.
Połączenie maszyn umożliwia również współpracę między nimi. Na przykład, jeśli jedna linia produkcyjna ma problemy z dostarczeniem odpowiednich materiałów do drugiej linii, to może wysłać automatyczne powiadomienie i poprosić o pomoc. To prowadzi do bardziej efektywnego wykorzystania zasobów i minimalizuje czas przestoju.
Warto również wspomnieć, że IoT umożliwia zdalne monitorowanie produkcji. Przez internet można śledzić postęp prac oraz otrzymywać powiadomienia w przypadku wystąpienia awarii lub innych problemów. Dzięki temu menedżerowie mogą szybko reagować i podejmować odpowiednie działania, co prowadzi do większej efektywności całego procesu produkcyjnego.
Ostatecznie, połączone maszyny w ramach Internetu Rzeczy mają ogromny potencjał do optymalizacji procesów produkcyjnych. Poprawa komunikacji między urządzeniami, zdolność do analizowania danych w czasie rzeczywistym oraz możliwość zdalnego monitorowania produkcji to tylko niektóre z korzyści wynikających z tej technologii.
Sztuczna Inteligencja w Fabryce – jak algorytmy poprawiają jakość i efektywność produkcji?
Sztuczna inteligencja (AI) jest kolejnym kluczowym elementem cyfrowej rewolucji w produkcji. Algorytmy oparte na AI są używane do analizy dużych ilości danych oraz podejmowania decyzji na podstawie tych informacji. W fabrykach sztuczna inteligencja może być wykorzystana do poprawy jakości produktów oraz efektywności procesów produkcyjnych.
Jednym z głównych zastosowań AI w fabryce jest kontrola jakości. Algorytmy mogą analizować dane dotyczące produktów, takie jak wymiary, kolor czy wykończenie, i porównywać je z ustalonymi standardami. Jeśli produkt nie spełnia określonych wymagań, system może automatycznie odrzucić go lub przekierować do dalszej inspekcji przez człowieka. Dzięki temu można zapewnić wysoką jakość produktów bez konieczności manualnej kontroli każdego elementu.
Sztuczna inteligencja może również być używana do optymalizacji procesów produkcyjnych. Algorytmy są w stanie analizować dane dotyczące wydajności maszyn oraz zużycia surowców i energii. Na podstawie tych informacji mogą proponować zmiany w ustawieniach maszyn lub harmonogramach produkcji, które prowadzą do większej efektywności i oszczędności.
Kolejnym obszarem wykorzystania sztucznej inteligencji jest prognozowanie awarii. Algorytmy mogą analizować dane historyczne oraz bieżące parametry pracy maszyn i na ich podstawie przewidywać możliwe problemy lub awarie. Dzięki temu można planować konserwację maszyn i unikać nieplanowanych przestojów, co ma istotny wpływ na efektywność produkcji.
Wnioskiem jest to, że sztuczna inteligencja ma ogromny potencjał do poprawy jakości i efektywności produkcji. Kontrola jakości, optymalizacja procesów oraz prognozowanie awarii to tylko niektóre z możliwości wynikających z wykorzystania algorytmów opartych na AI w fabryce.
Automatyzacja na Wysokich Obrotach – praktyczne zastosowania robotyki w produkcji
Robotyka jest jednym z najbardziej widocznych aspektów cyfrowej rewolucji w produkcji. Automatyzacja procesów przy użyciu robotów może znacznie poprawić efektywność oraz precyzję działań w fabryce.
Jednym z kluczowych obszarów automatyzacji jest linia montażowa. Roboty mogą być programowane do wykonywania powtarzalnych czynności, takich jak skręcanie śrub czy montaż elementów. Dzięki temu można osiągnąć większą dokładność oraz szybkość wykonania tych operacji. Ponadto, roboty są również bardziej odporne na zmęczenie niż ludzie, co pozwala utrzymać wysoką wydajność przez dłuższy czas.
Kolejnym praktycznym zastosowaniem robotyki jest magazynowanie i logistyka. Roboty mogą być wykorzystane do przenoszenia, sortowania oraz pakowania produktów. Dzięki temu można zoptymalizować procesy magazynowe i skrócić czas potrzebny na przygotowanie zamówień.
Warto również wspomnieć o współpracy człowiek-robot. W niektórych fabrykach ludzie i roboty pracują razem, dzieląc się różnymi zadaniami. Na przykład, człowiek może być odpowiedzialny za zadania wymagające dużej precyzji lub kreatywności, podczas gdy robot wykonuje powtarzalne operacje. Taka współpraca pozwala na wykorzystanie najlepszych cech zarówno maszyny jak i człowieka.
Ostatecznie automatyzacja przy użyciu robotów ma wiele korzyści dla produkcji. Poprawa efektywności, większa dokładność oraz możliwość pracy w trudnych warunkach to tylko niektóre z nich.
Big Data dla Przemysłu – jak analiza danych wpływa na doskonałość jakościową
Analiza danych (Big Data) stała się kluczowym narzędziem w dzisiejszym przemyśle. Duże ilości informacji generowanych przez różne systemy produkcyjne mogą być analizowane w celu poprawienia jakości produktów oraz procesów produkcyjnych.
Jednym z głównych obszarów, w których analiza danych ma duże znaczenie, jest kontrola jakości. Dane dotyczące parametrów produkcji i cech produktów mogą być analizowane w czasie rzeczywistym. Na podstawie tych informacji można identyfikować potencjalne problemy lub odchylenia od ustalonych standardów jakości. Dzięki temu możliwe jest szybkie reagowanie i podejmowanie odpowiednich działań korygujących.
Analiza danych może również pomóc w optymalizacji procesów produkcyjnych. Przez monitorowanie wydajności maszyn oraz zużycia surowców i energii można identyfikować obszary, w których można wprowadzić zmiany mające na celu poprawę efektywności. Na przykład, jeśli okazuje się, że pewien rodzaj surowca powoduje większe zużycie energii niż inne, to można rozważyć jego zamianę na bardziej ekonomiczną alternatywę.
Warto również wspomnieć o predykcyjnej analizie danych. Algorytmy mogą analizować dane historyczne oraz bieżące parametry pracy maszyn i na ich podstawie przewidywać możliwe awarie lub problemy. Dzięki temu możliwe jest planowanie konserwacji maszyn i unikanie nieplanowanych przestojów produkcji.
Wnioskiem jest to, że analiza danych ma ogromny potencjał do poprawy jakości produktów oraz efektywności procesów produkcyjnych. Kontrola jakości w czasie rzeczywistym, optymalizacja produkcji oraz predykcyjna analiza awarii to tylko niektóre z możliwości wynikających z wykorzystania Big Data w przemyśle.
Wirtualne Technologie w Fabryce – jak symulacje i modelowanie podnoszą standardy efektywności
Wirtualne technologie są kolejnym ważnym elementem cyfrowej rewolucji w produkcji. Symulacje komputerowe i modelowanie 3D mogą być wykorzystane do projektowania nowych linii produkcyjnych, testowania różnych scenariuszy oraz doskonalenia istniejących procesów.
Jednym z głównych obszarów wykorzystania wirtualnych technologii jest projektowanie fabryki. Przed rozpoczęciem budowy nowej fabryki można przeprowadzić symulację komputerową, która pozwoli ocenić różne aspekty planowanego zakładu. Na przykład, można sprawdzić optymalną lokalizację maszyn czy rozmieszczenie stanowisk pracy dla minimalizacji czasu potrzebnego na transport materiałów.
Symulacje komputerowe mogą również pomóc w doskonaleniu istniejących procesów produkcyjnych. Można przetestować różne scenariusze i zmiany, takie jak wprowadzenie nowej maszyny czy zmiana kolejności operacji. Dzięki temu można znaleźć optymalne rozwiązania, które prowadzą do większej efektywności i oszczędności.
Wirtualne technologie mogą być również wykorzystane do szkolenia pracowników. Przy użyciu symulacji komputerowych można nauczyć operatorów obsługi nowych maszyn lub zapoznać ich z procedurami bezpieczeństwa. To pozwala zaoszczędzić czas i koszty związane ze szkoleniem w rzeczywistości.
Ostatecznie, wirtualne technologie mają duży potencjał do podnoszenia standardów efektywności w produkcji. Projektowanie fabryki, doskonalenie procesów oraz szkolenie pracowników to tylko niektóre z możliwości wynikających z wykorzystania symulacji i modelowania 3D.